News & Updates
Methods to optimize container traffic
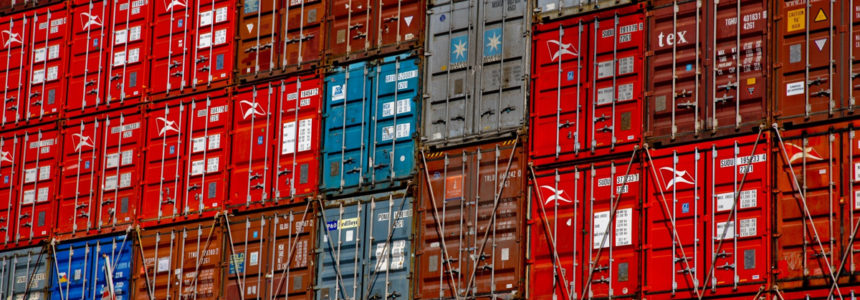
There are no winners in the game of stagnant port containers. Companies lose money by incurring penalty fees. Congested ports aren’t able to optimize capacity. Even penalty payments fail to offset the cost of slow and sluggish container traffic.
Leaving containers to sit in ports is no small matter: Worldwide, TEU (20-feet equivalent unit) container port traffic exceeded 792 million in 2018. When container pickups get delayed beyond the several day grace periods that ports avail as a free pickup window, penalty charges can reach up to $150 a day.
Managers hoping to optimize their container traffic lack visibility of actual and potential container delays. And the fees keep adding up, day by day. Further complicating matters is that every port, transporter, and shipper have its tracking system, so information isn’t readily exchanged or updated in promptly. If managers had a way to see in real time what was going on with every container in every port and transfer point, they could improve results and reduce penalty fees.
Change the game with real-time reporting
Imagine this: A logistics team is searching through reports while calling warehouses and drayage companies in a frantic attempt to get containers picked up the same day. Why? Because the highly critical process of reconciling which containers have left the port happens to be a manual one. The team has just realized that last Friday’s pickup was from new arrivals versus containers that have reached maximum free time.
Historically, warehouse (WMS) and enterprise resource management systems neglect yard and port tracking applications. As a result, it is common for ports, transporters and shippers to resort to “home grown” container traffic tracking systems. These legacy operations often make it impossible to exchange real time information across disparate systems quickly.
This DIY approach is further exacerbated when managers create their own spreadsheets that track container drayage stats, manually updating information in a best attempt to stay on top of penalty fees.
What if there were a way to integrate the many disparate container tracking systems that ports, yards, transporters and shippers all manage, control, and automate the information flows from system to system so everyone has the latest real time information on their containers?
For companies managing the flow of containers off the port, this would be a game changer in their operations and their budgets.
Ways to integrate
One way to get disparate systems to talk to one another is by using a cloud-based universal portal that companies sign into, and that would integrate all of the diverse backend systems used to track containers by different ports, shippers, transporters, etc. With a system like this, the software would interface these systems through a series of APIs (application programming interfaces). Everyone would have secure access through the portal to the information that they needed.
A second option is the use of integration software that can interface a company’s container tracking system with systems used by other parties to a container transaction that is relevant to the company. The backend integration software automatically pulls in data from the different business partner systems, updates the system, and does it all in real time.
With integrated systems, what information would a container manager have at his or her immediate disposal?
Several come to mind:
- Every container out in the field would be identified by its unique number and also to the port where the container is presently stored.
- Each container would have the number of “free” days it was allowed to stay in port, and the amount of the storage and demurrage penalty fees that the port charges for a container overstay.
- Total charges for each container’s storage in the port would be automatically incremented with each day’s storage and demurrage penalty fees at the time that it was charged.
- Any container placed on a customs hold, which increases the likelihood of the container leaving a port late and incurring penalty fees, would be identified.
- A manager would be able to see which ports (and containers) were incurring the most penalty fees and overstays.
Valuable real-time data like the above could be aggregated and developed into operational reports that managers would review for decision making: Should I reroute containers to less active ports? Or find backup transporters in cases where containers were regularly being left in ports too long or not returned? With the right information, the possibilities are endless.
Numbers don’t lie
Over the past three years, global container demand has steadily grown, averaging an annual growth rate of 4.7 percent. If a shipping company with just 2,000 containers annually experiences five percent of its containers being delayed for three days in ports at an average of $100 per day, demurrage penalties paid on that five percent of containers would amount to $30,000 of unplanned expenses. That doesn’t even begin to account for the penalty fees accrued in ports for container detentions, when containers are not returned in timely fashion to the ports from which they are picked up.
This is a lot of money to lose for a “non-moving” part of the supply chain that isn’t flowing —and it comes as no surprise that container penalty fees are a continuous supply chain pain point for shippers, transporters and ports. Hand-cobbled spreadsheets can’t address multimillion dollar problems.
A universal data and integration solution that can pull together all parties’ systems into one interface, with each party accessing a “single version of the truth,” is what’s needed.
If that can’t be achieved, it’s incumbent on individual shippers, transporters and port managers to develop their own integration solutions so they can easily interface with other external systems.
What’s not acceptable is routinely baking in cost numbers into annual budgets to account for anticipated container delays and accepting these delays as a way of life.
About the Author
Laura Pullins is the director of digital supply chain for HULFT, a comprehensive data logistics platform that helps IT quickly find, secure, organize, transform, and move the right information.
With over two decades of experience in operations and supply chain, Laura works closely with organizations to help them identify their most urgent technology problems, and then implement a productive, cost-effective strategy that is built for the future.
Her background spans manufacturing, warehousing operations, inventory control, and international trade. Laura has been responsible for all modes of domestic and international transportation including full air charters and heavy lift vessels.